I haven't been able to spend a lot on the router lately partially because I have had parts on order and I've just had so many other things going on.
I spent some time today back tracking a little bit. I had dumped a full linear bearing worth of balls on the floor by inadvertantly pulling the rail out and lost a few.. these needed to be replaced which meant taking the Z axis all apart. Other issues abound.
Here are pics from today. I had to leave because it was so hot and I am still waiting (six months) for windows and hence AC. I have two free days left in the week and plan on being done with the Z and finish machining parts for the X axis as well.
Tuesday, July 19, 2011
Saturday, July 16, 2011
A new Welder in the Family
My son decided he had to learn how to weld this morning. So I gave him a few pointers, a mask and gloves and let him go to it.
Here are a few pics.
Here are a few pics.
Friday, July 15, 2011
Milling Machine is up and running!
I thought I had the mill together and working and found that the knee would rock a little when taking heavy cuts. The knee lock also wasn't working so well and I had broken motor mounts. I took the time to look up repairs online and progressively fixed them. Most of the repairs were made using parts fabricated or modified on mill or lathe.
Another shot of the mill in use. I haven't used a boring head in a while and managed to only burn out one bar. This is the router mount in progress.
Sunday, July 3, 2011
Follow up to new milling machine
Here are some follow on pics.
I've slowly been cleaning it up and painting it. I still have some work around the base and detailing. I only primed and epoxied it.. we'll see how long it lasts. A close up of the head after paint is below, It ended up being easier to just remove some parts after the fact and clean them rather than removing them and taping the holes. I chose off white because that is the color I had seen in R&D shops as a kid.
I've slowly been cleaning it up and painting it. I still have some work around the base and detailing. I only primed and epoxied it.. we'll see how long it lasts. A close up of the head after paint is below, It ended up being easier to just remove some parts after the fact and clean them rather than removing them and taping the holes. I chose off white because that is the color I had seen in R&D shops as a kid.
Friday, June 17, 2011
New (to me) Milling machine
I rigged this out of an upper floor yesterday. I was able to clean it up in a few hours, adjust the gibs and get it close to where I want it with a pallet jack. I'll drop it to the floor, bolt and wire it next week.
I can't tell you how cool it feels to own a Bridgeport.. I have wanted one my whole life so to be able to get one at no cost and learn the in's and out's of it by having to take it apart was just amazing! I am looking for collets, fly cutters, chucks etc. today and hope to have it up and running soon. It'll sure beat a grinder and little drill press.
Pic of Mill being disassembled and rigged out.
I can't tell you how cool it feels to own a Bridgeport.. I have wanted one my whole life so to be able to get one at no cost and learn the in's and out's of it by having to take it apart was just amazing! I am looking for collets, fly cutters, chucks etc. today and hope to have it up and running soon. It'll sure beat a grinder and little drill press.
Pic of Mill partially reassembled and cleaning underway.
Friday, June 10, 2011
Hoverbike Concept
hoverbike prototype
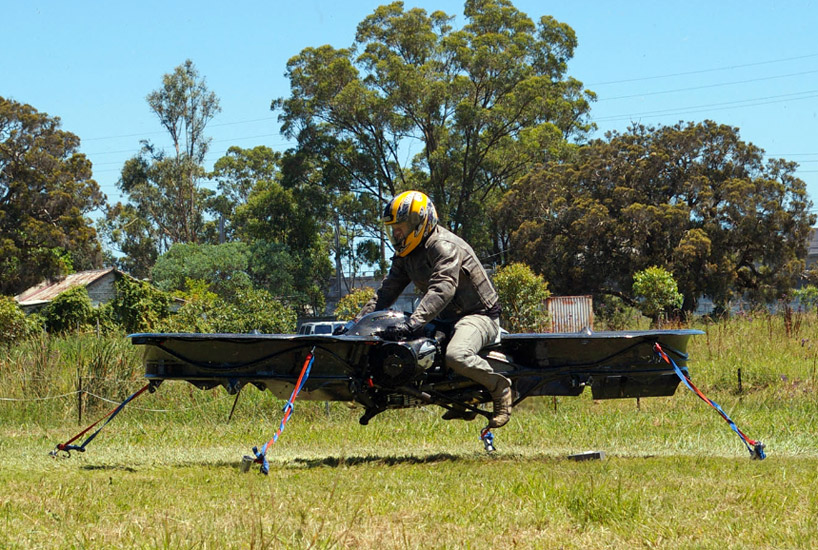
'hoverbike' prototype, invented by australian mechanical engineer chris malloy
working in his spare time, australian mechanical engineer chris malloy claims to have invented a working 'hoverbike',
operated like a motorcycle. measuring 9.8 long by 4.3 wide and 1.8 feet high (3 x 1.3 x 0.55m) the prototype bike
seats a single pilot between two oak and carbon fibre-blade two-blade propellers, currently exposed but which
for safety reasons will be covered in mesh in future models. in basic flight design, the bike is modeled after
tandem-rotor chinook helicopters, whereby the two rotors rotate in opposite directions, canceling one another's torque
and thus increasing stability and efficiency of the vehicle.
the 'hoverbike' is controlled completely by handlebars, via actions similar to those used for motorcycles. forward and reverse
movement is accomplished through two grips, one of which increases the thrust while the other adjusts the angle of the control vanes
positioned below the rotors, pitching the nose of the vehicle down for forward movement and up for backwards.
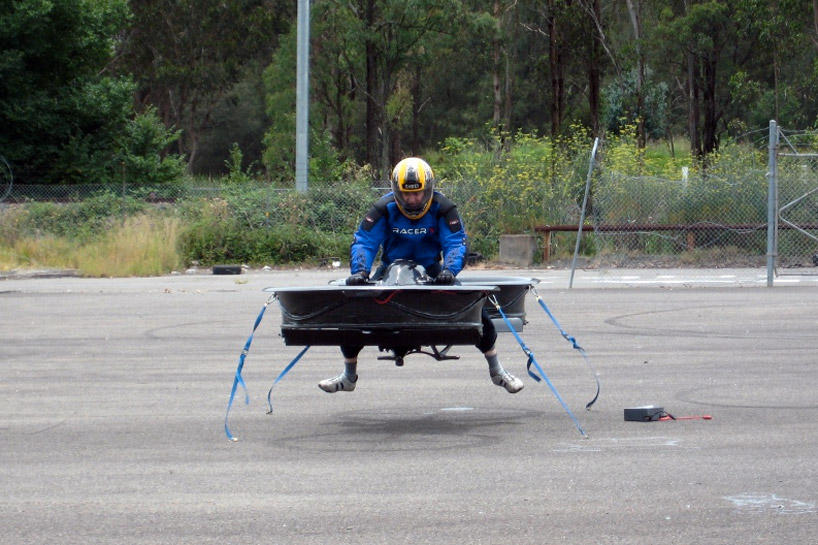
front view during tethered testing
malloy estimates that the 'hoverbike', whose 4-stroke engine drives 80kW of power to the propellers, generating 7500rpm,
is capable of reaching heights of over 10,000 feet and of traveling 150 knots (173mph, or 278km/h). the vehicle's 30L primary tank
can be supplemented with additional fuel storage but even on its own should offer a range of 92 miles (148km) when traveling
at 80 knots (92mph or 148km/h).
although the relatively low number of parts makes the craft simpler and more reliable than most helicopters,
safety concerns for the bike have led malloy to make most engine and operating features triply redundant.
two explosive parachutes can be attached to the vehicle's frame, although malloy recommends that the pilot
simply wear an emergency parachute so that he has the option of dislodging from the vehicle if necessary.

full profile view

3/4 top view

aerial view, placed next to a car for size reference
with tests already conducted of the prototype tethered to the ground, the first flight tests are planned for the coming months.
the 'hoverbike' is classified in the united states as an 'ultralite' vehicle, meaning that it would not require a pilot's license
to be operated. malloy hopes to begin limited production of the bike within a year, estimating the cost at about 40,000 USD
for a run of 100 units per year, and on par with performance motorcycles if demand rises to about 1000 units per year.
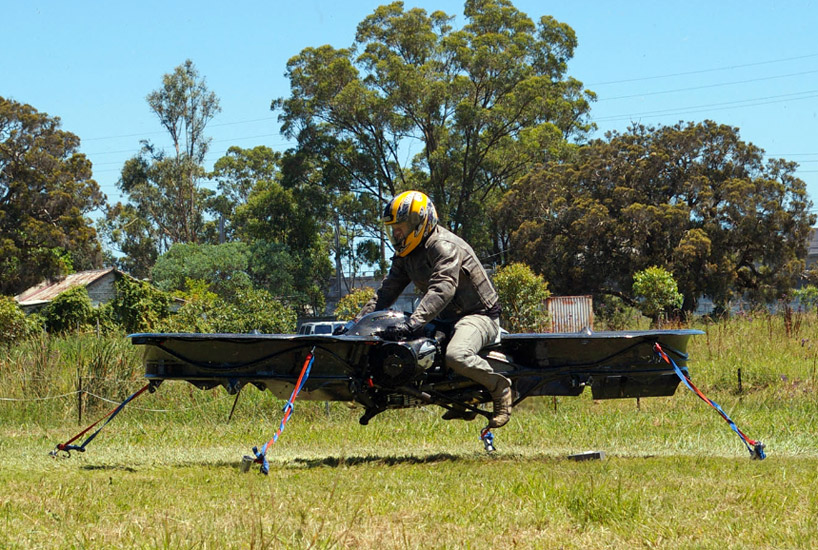
'hoverbike' prototype, invented by australian mechanical engineer chris malloy
working in his spare time, australian mechanical engineer chris malloy claims to have invented a working 'hoverbike',
operated like a motorcycle. measuring 9.8 long by 4.3 wide and 1.8 feet high (3 x 1.3 x 0.55m) the prototype bike
seats a single pilot between two oak and carbon fibre-blade two-blade propellers, currently exposed but which
for safety reasons will be covered in mesh in future models. in basic flight design, the bike is modeled after
tandem-rotor chinook helicopters, whereby the two rotors rotate in opposite directions, canceling one another's torque
and thus increasing stability and efficiency of the vehicle.
the 'hoverbike' is controlled completely by handlebars, via actions similar to those used for motorcycles. forward and reverse
movement is accomplished through two grips, one of which increases the thrust while the other adjusts the angle of the control vanes
positioned below the rotors, pitching the nose of the vehicle down for forward movement and up for backwards.
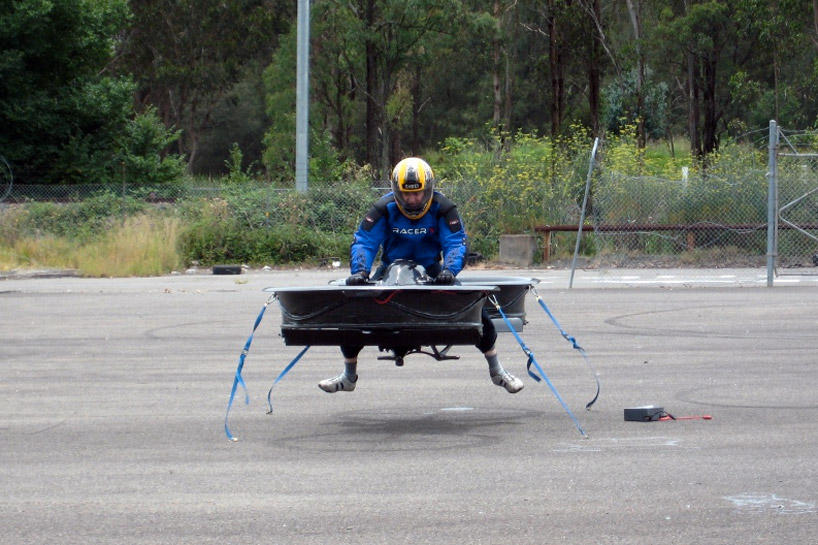
front view during tethered testing
malloy estimates that the 'hoverbike', whose 4-stroke engine drives 80kW of power to the propellers, generating 7500rpm,
is capable of reaching heights of over 10,000 feet and of traveling 150 knots (173mph, or 278km/h). the vehicle's 30L primary tank
can be supplemented with additional fuel storage but even on its own should offer a range of 92 miles (148km) when traveling
at 80 knots (92mph or 148km/h).
although the relatively low number of parts makes the craft simpler and more reliable than most helicopters,
safety concerns for the bike have led malloy to make most engine and operating features triply redundant.
two explosive parachutes can be attached to the vehicle's frame, although malloy recommends that the pilot
simply wear an emergency parachute so that he has the option of dislodging from the vehicle if necessary.

full profile view

3/4 top view

aerial view, placed next to a car for size reference
with tests already conducted of the prototype tethered to the ground, the first flight tests are planned for the coming months.
the 'hoverbike' is classified in the united states as an 'ultralite' vehicle, meaning that it would not require a pilot's license
to be operated. malloy hopes to begin limited production of the bike within a year, estimating the cost at about 40,000 USD
for a run of 100 units per year, and on par with performance motorcycles if demand rises to about 1000 units per year.
Wednesday, June 8, 2011
Autodesk Photofly results
I recently discovered Autodesk Photofly and gave it a try. below are the results. It took a couple of attempts but is relatively easy to use even for a novice. I am going to play with some of the dimensional qualities of these models and then attempt to rout in 3D.. this is very exciting and replaces thousands of dollars worth of equipment if even close to being dimensionally accurate.
Monday, May 16, 2011
Last weeks new shop additions
Last week I was able to pick up some new (to me) tools from another tenant in my building. They included a big gear driven powermatic scroll saw, an oscillating drum sander (4hp!) an old Atlas/Craftsman drill press a commercial paper shear ( i will use it for composites and veneers.) and a 50" x 50" x 2"+ solid maple bench top.
I am now starting to run out of room and need to optimize.


I am now starting to run out of room and need to optimize.



Friday, May 6, 2011
visual machine via DesignBoom
todd mclellan: disassembly
published 05.06.11

published 05.06.11

by carefully taking apart and arranging every piece and component of an old and often iconic relic, the series is an abstract portrait of an era of mechanical craft that we have seemingly left behind.
Thursday, April 14, 2011
"Construction Toy" by Wouter Scheublin Lego's for functional projects!
A recent Post by Wouter Scheublin where he debut's his " Construction Toy" concept. I will add this to my long list of things to build. more info on this and other designs by Wouter can be found at http://www.wouterscheublin.com







Monday, April 11, 2011
Z axis Initial design
I sat down for a few hours and reviewed my drawings for the Z (vertical) axis and decided to beef it up since I want this to be a quasi-gantry mill. ( ie, capable of medium duty milling ) I decided to do away with the original guides and get some square NSK's. I am trying hard to maintain a +- .005" tolerance and I figured they would make it easier.
Note the salvaged metal being used. I know it looks tacky, but it is free and believe it or not was machined flat/square and in some cases ground before being powder coated..
Note the guides have been oriented in two planes instead of the usual single plane so they can reduce deflection in two axis.. That is 3/8" channel and angle being used!
Pinewood derby races are this week so I probably won't post until next.
Note the salvaged metal being used. I know it looks tacky, but it is free and believe it or not was machined flat/square and in some cases ground before being powder coated..
Note the guides have been oriented in two planes instead of the usual single plane so they can reduce deflection in two axis.. That is 3/8" channel and angle being used!
Pinewood derby races are this week so I probably won't post until next.
Completion of Y axis!
So this is it for the Y mechanicals. I designed the parts on sketch up and had them made ($20/pc!) the turn around was about a week out of florida.
here are the blanks before assembly.
Here they are after assembly with the motors and couplings attached.
No I only have the X and Z to complete!!
here are the blanks before assembly.
Here they are after assembly with the motors and couplings attached.
No I only have the X and Z to complete!!
Sunday, April 3, 2011
RepRap Entry
I just entered the Protobot in the RepStrap area at RepRap.org I want to explain the Rep-Strappedness of the machine to any who may venture here.
I built the majority of this machine from parts liberated from an italian hair sorting machine that was being scrapped. It is considered Version B, Unit 0.1 because it is what my brother ( musings in futility ) and I consider to be a mid-sized machine. We want to build a Version A, which will be something like a Ultimaker or a Janome JSG where there are redundant guides on upper (X,Y) axis.
Claimed innovations in our design include the redundant guides coupled with the fact that the machine will be capable of reproducing itself in metal. We will also go to the effort of creating a process of creating metal parts from base material ( ie, aluminum cans ) as well as plastic parts from base material that has one way or another been taken from previously used material.
VB0.1 will be self reproducing and capable of the following:
3D scanning with physical probe and/or a laser scanner
Routing wood, composites and plastics.
Cutting stencils, vinyl and other sheet material with Vacuum hold down.
Cutting Foam using hot knife process.
Performing typical Cartesian Robot functions
Plotting using a typical pen plotter as well as traditional human implements ( pencil, markers, brushes.)
Light milling to include aluminum and light steel
Many processes exist in metal working that I feel have not been exploited by the RepRap community. These include the use of low temperature alloys, DIY lost foam metal casting, electroforming etc. Our work will parallel the RepRap community in the sense that VB0.1 for example will use metal taken from recycled sources and utilize it for self duplication and creation of it's younger, smaller sibling ( VA0.1 ) which will go on to self duplicate..
My major argument being that I don't see the difference between a machine that can duplicate itself in metal ( which is 100% recyclable) and a machine that is duplicating itself with plastic and metal parts that are not sustainably created. furthermore the PROTOBOT series will have a higher content of parts that are self created compared to COTS ( commercial off the shelf )
I have seen a lot of RepRap users of late build parts for the purpose of repairing previously made parts because the plastic has certain wear characteristics. this will not be the case using aluminum or other machined composite parts.
JOSH
I built the majority of this machine from parts liberated from an italian hair sorting machine that was being scrapped. It is considered Version B, Unit 0.1 because it is what my brother ( musings in futility ) and I consider to be a mid-sized machine. We want to build a Version A, which will be something like a Ultimaker or a Janome JSG where there are redundant guides on upper (X,Y) axis.
Claimed innovations in our design include the redundant guides coupled with the fact that the machine will be capable of reproducing itself in metal. We will also go to the effort of creating a process of creating metal parts from base material ( ie, aluminum cans ) as well as plastic parts from base material that has one way or another been taken from previously used material.
VB0.1 will be self reproducing and capable of the following:
3D scanning with physical probe and/or a laser scanner
Routing wood, composites and plastics.
Cutting stencils, vinyl and other sheet material with Vacuum hold down.
Cutting Foam using hot knife process.
Performing typical Cartesian Robot functions
Plotting using a typical pen plotter as well as traditional human implements ( pencil, markers, brushes.)
Light milling to include aluminum and light steel
Many processes exist in metal working that I feel have not been exploited by the RepRap community. These include the use of low temperature alloys, DIY lost foam metal casting, electroforming etc. Our work will parallel the RepRap community in the sense that VB0.1 for example will use metal taken from recycled sources and utilize it for self duplication and creation of it's younger, smaller sibling ( VA0.1 ) which will go on to self duplicate..
My major argument being that I don't see the difference between a machine that can duplicate itself in metal ( which is 100% recyclable) and a machine that is duplicating itself with plastic and metal parts that are not sustainably created. furthermore the PROTOBOT series will have a higher content of parts that are self created compared to COTS ( commercial off the shelf )
I have seen a lot of RepRap users of late build parts for the purpose of repairing previously made parts because the plastic has certain wear characteristics. this will not be the case using aluminum or other machined composite parts.
JOSH
Friday, April 1, 2011
X axis final Rev linear guides/bearings installed
Todays work, I had previously installed round shafts and guides but felt they moved too much. These do not move at all with several hundred lbs on them.
Here it is in detail. ( note chunk of aluminum is being used as an alignment guide and will be replaced by solid bracket with Z axis attached.)
Here it is in detail. ( note chunk of aluminum is being used as an alignment guide and will be replaced by solid bracket with Z axis attached.)
Wednesday, March 30, 2011
A little welding and paint
Recent pics of PROTOBOT VB0.1.
I decided to use the original stand to support the Lathe, so I could make a purpose built one for the protobot.
Here are some progress pics.
I hope the green isn't too much. I got the color to match the lathe and decided to start making everything this color. It'll end up with a lot of contrasting components on it so it should be O.K.
I decided to use the original stand to support the Lathe, so I could make a purpose built one for the protobot.
Here are some progress pics.
I hope the green isn't too much. I got the color to match the lathe and decided to start making everything this color. It'll end up with a lot of contrasting components on it so it should be O.K.
Monday, March 28, 2011
The Lathe
I got this little Craftsman/Atlas 12" x 36" lathe a few years ago and am just now setting it up. I tried turning some little brass chunks I have laying around and broke a few cutters.. I guess practice is in order., I was able to turn the piece down and part it, take it to size but think the lathe has a bit of spring in it. I have abase for it and will have it in it's permanent position in the next week ( once the ProtoBot base is complete and out of the way.)
I have a spinning attachment, milling attachment, all sorts of dogs, assymetrical turning devices, a back blate, two three jaw chucks and a four jaw chuck. I am looking for a collet chuck and a better milling attachment.
I have a spinning attachment, milling attachment, all sorts of dogs, assymetrical turning devices, a back blate, two three jaw chucks and a four jaw chuck. I am looking for a collet chuck and a better milling attachment.
A new Base
I have been building the machine on the floor for some time now as I did not have enough bench space and didn't want to weld/grind on the bench space I have. Now that I am almost entirely into a assembly stage I felt it necessary to build a base. This is a stitched picture so there is a flaw, ( see if you can find it.)
I built it upside down and plan to weld it up, paint the underside, flip it over and repaint. You will notice the leg arrangement is a little weird. I skewed the legs so that I could fit full size workpieces, excess stock and oversized parts on the lower tray.. The idea is to be able to cut a very large parts from below, I am particularly interested in mortises/tenons on seats, large aircraft models etc.
I built it upside down and plan to weld it up, paint the underside, flip it over and repaint. You will notice the leg arrangement is a little weird. I skewed the legs so that I could fit full size workpieces, excess stock and oversized parts on the lower tray.. The idea is to be able to cut a very large parts from below, I am particularly interested in mortises/tenons on seats, large aircraft models etc.
Sunday, March 6, 2011
Andromeda CNC out of Australia
I found this site recently. Their work roughly parallels mine in many ways.
http://www.projectandromeda.com.au/blog/?p=30
CNC Machine Design and Construction Highlights
Everyone should have a CNC machine. Or at least everyone building a UAV should try and get one. They are such useful tools and one can never know unless you have one at your disposal. To create the Project Andromeda aircraft, Damien and I embarked on building a relatively large CNC machine. Large enough to create our wing molds. We agreed on a 2mx1m overall dimension and began planning.
Damien took the helm by drafting up the initial layout of the machine. We visited a local aluminium distributor and Damien promptly drafted their entire catalog into AutoCAD. This step proved to be a lifesaver as we could never have put everything together without the simplicity of selecting stock within AutoCAD. By this stage all our components had arrived. The 2m long X axis ballscrew, the 3 4.5kg motors that would drive the ballscrews and the 5kg spindle. Damien’s initial design was maturing and by this stage all our measurements were in CAD.
It was around this time that my curiosity got the best of me and I managed to dislodge the ball bearings out of the Z axis ballnut/ballscrew assembly while tinkering with it. Little did I know that this would start a saga of misery that would only see closure by the perseverance of Damien in figuring out how to “reball” a ballnut: an apparently impossible task.
The Z axis proved to be the hardest section to design and build. The spindle was very heavy and we needed to keep things close in order to limit the moment arm imposed onto the ballscrew assembly. Damien came up with a very tight design that can be seen below:
The spindle is almost touching the Z axis ballscrew with only a couple of millimeters to spare. Another tight fit is the Y axis ballnut visible near the bottom of the spindle. Its circumference just clears the Z axis ballscrew leaving a tight fit that allows as much movement as possible for the gantry. The picture below shows the clearance at the front of the gantry, which is about 2mm. This allows the Y axis to be sized down as well, increasing the X axis working area.
After the painstaking task of assembling the Z-Y axes, we finally moved on to the X axis which proved to be almost as hard. The process of making sure the 2m long fully supported rails were parallel and perpendicular to each other and the table almost exhausted our patience. This was a necessary evil as we wanted to ensure we could realise as much of the theoretical 10 um accuracy as possible. Once elevated we mounted the Y-Z gantry and turned on the motors for the first time. The authority with which the 80V DC motors moved the gantry was beyond our highest expectations.
The final assembly took a while, and there were some issues with the single sided X axis drive, but these issues were mostly because of the lack of cross bracing between the X axes. Once these issues were alleviated, the construction of the machine looked all but complete. Meanwhile I had made some headway with the motor drive and computer interface circuitry. I will cover these stories in a future article.
Monday, February 28, 2011
Protobot and self replication
A few people have asked about the purpose of this machine and why certain features exist. So I have some explaining to do.
It is interesting to follow the history and evolution of industrial machinery. ( please correct me if I mess up here.) First of all there were archaic tools, these were used to make more and more precise hand tools, which were eventually used to make simple machines. Simple machines were used to make essentially the first drilling machine. drilling machines evolved into the drill press and later the lathe. All sorts of other machines were being designed in other veins. Eventually drill presses evolved into the lathe and the lathe had a sort of vertical crossfeed attached that allowed a person to mill. Drill presses were beefed up and the same crossfeed mechanisms installed to make a milling machine. Milling machines and lathes have evolved exponentially since then primarily in times of extreme need ( Industrial revolution and many wars really helped.)
At this point these machines are very complicated and proprietary, I was at a machinery dealers a few weeks ago who had mills and lathes that you could easily put a car in. I asked him about business and what he generally had difficulty obtaining. He said the biggest issue he has is with proprietary equipment on these machines, to make matters worse he knows that a lot of the parts he is looking at are the same as what are on other machines but he can't buy them for fear of voiding warrantees, losing support etc.
Here's my point:
Yes this machine will be proprietary, but we plan on making everything readily available including the designs and part sources in the hopes that others will be able to obtain them and use them. Furthermore, We hope to use this machine to make other better machines just like old times. As an example, one of my biggest costs was making up the frames ( base and X/Y subframe.) I looked around and it would have been very difficult to get good castings at a good price so we ended up using metal from the hair sorting machine for these parts. When the machine is done i'll be able to route out wooden parts and take them to the caster, have them cast, certain areas ground and be able to provide a part that is +- .0005" rather than the +-.006 that we are struggling to maintain now. This is the difference between a homemade device and a world class machine. The same will be true of almost all components except ball screws, nuts and linear bearings/guides. This will drop my costs by thousands of dollars and allow me to provide them reasonably.
Sorry for the diatribe.
It is interesting to follow the history and evolution of industrial machinery. ( please correct me if I mess up here.) First of all there were archaic tools, these were used to make more and more precise hand tools, which were eventually used to make simple machines. Simple machines were used to make essentially the first drilling machine. drilling machines evolved into the drill press and later the lathe. All sorts of other machines were being designed in other veins. Eventually drill presses evolved into the lathe and the lathe had a sort of vertical crossfeed attached that allowed a person to mill. Drill presses were beefed up and the same crossfeed mechanisms installed to make a milling machine. Milling machines and lathes have evolved exponentially since then primarily in times of extreme need ( Industrial revolution and many wars really helped.)
At this point these machines are very complicated and proprietary, I was at a machinery dealers a few weeks ago who had mills and lathes that you could easily put a car in. I asked him about business and what he generally had difficulty obtaining. He said the biggest issue he has is with proprietary equipment on these machines, to make matters worse he knows that a lot of the parts he is looking at are the same as what are on other machines but he can't buy them for fear of voiding warrantees, losing support etc.
Here's my point:
Yes this machine will be proprietary, but we plan on making everything readily available including the designs and part sources in the hopes that others will be able to obtain them and use them. Furthermore, We hope to use this machine to make other better machines just like old times. As an example, one of my biggest costs was making up the frames ( base and X/Y subframe.) I looked around and it would have been very difficult to get good castings at a good price so we ended up using metal from the hair sorting machine for these parts. When the machine is done i'll be able to route out wooden parts and take them to the caster, have them cast, certain areas ground and be able to provide a part that is +- .0005" rather than the +-.006 that we are struggling to maintain now. This is the difference between a homemade device and a world class machine. The same will be true of almost all components except ball screws, nuts and linear bearings/guides. This will drop my costs by thousands of dollars and allow me to provide them reasonably.
Sorry for the diatribe.
Play and used parts
I didn't get much of a chance to work on the Protobot last week but a lot has happened.
First, I discovered after adding the Z (vertical) axis that I have a little play in the X (side to side) axis. One of the problems with using salvaged material is that stuff like this happens. Fortunately I have better guides but they are a few inches shorter and will require some add'l machining ( which I am doing by hand right now.) No problem.. If the tolerances weren't so tight I wouldn't have worried about it. but .0125" play can add up as well as cause vibration and mechanical feedback issues in the machine itself. I'll be able to use the current X guides for a less precise machine later.
I have a few customers already, but can't talk about either one.. bummer. maybe once I've developed a better relationship with them. The friend I made at the USPTO is evidently using the parts I gave him for his invention so progress is being made on other fronts.
First, I discovered after adding the Z (vertical) axis that I have a little play in the X (side to side) axis. One of the problems with using salvaged material is that stuff like this happens. Fortunately I have better guides but they are a few inches shorter and will require some add'l machining ( which I am doing by hand right now.) No problem.. If the tolerances weren't so tight I wouldn't have worried about it. but .0125" play can add up as well as cause vibration and mechanical feedback issues in the machine itself. I'll be able to use the current X guides for a less precise machine later.
I have a few customers already, but can't talk about either one.. bummer. maybe once I've developed a better relationship with them. The friend I made at the USPTO is evidently using the parts I gave him for his invention so progress is being made on other fronts.
Recent macro shot of machine
Y axis ball screws being added to machine
Close up of Y axis screw. I got these on Ebay for $100/pc.
I went to try and get parts and found out they were $600 screws and that it would be cheaper to just get other used ones. Fortunately I was able to rebuild what I had. This is common when re-using material, and the next step is to typically try and source less expensive assemblies. The problem then becomes buying overseas or finding a good source for good, inexpensive stuff in the U.S. I have found several and am working on a list to add to the Protobot Industries page. https://sites.google.com/site/protobotindustries
Sunday, February 13, 2011
X axis work
I've just started on the X axis and found I needed parts from McMaster Carr. So the parts are on order and I am working on the drive side of the Y axis. It turned out I had some nice angle brackets from the hair blending machine that I could modify a little to work. Pictures follow.
On a side note I've been working on a patent for another idea and had the chance a few months ago to go to the USPTO for a weekend to attend some workshops. I met a lot of people and made some good conections, I also met David Kappos who is the USPTO chief. I have to admit unless they are blowing smoke you know where their set-up seems to be really transparent and straightforward. Most of my questions were answered and I came away feeling like the process was very manageable and that I could do most of the work myself ( an exception being some legal writing) I am now in the process of writing up three provisional applications with the hopes of being able to try and commercialize before committing to the cost of the full blown patent.
On a side note I've been working on a patent for another idea and had the chance a few months ago to go to the USPTO for a weekend to attend some workshops. I met a lot of people and made some good conections, I also met David Kappos who is the USPTO chief. I have to admit unless they are blowing smoke you know where their set-up seems to be really transparent and straightforward. Most of my questions were answered and I came away feeling like the process was very manageable and that I could do most of the work myself ( an exception being some legal writing) I am now in the process of writing up three provisional applications with the hopes of being able to try and commercialize before committing to the cost of the full blown patent.
Adding Y axis
I took a couple of angles sections of steel out of the hair blending machine and used them for uprights. My brother and I had debated on this, he won out on the dual motor design which will give the machine less of a chance of kicking out of square. I won out because I can still take all of the bases out of the machine and really tall parts that are on the ground or install a vacuum base, the scanning bed etc. etc. as I wanted.
Here are a few pics of the base with the Y axis and uprights for the X and Z axis.
Here are a few pics of the base with the Y axis and uprights for the X and Z axis.
Change of plans
I got to looking at the design I had and all the new materials that I received from my landlord and decided to change some things up. The overhead cartesian idea had been born out of a desire to have long continuous square tube supports and minimized flex in any axis. The machine I took apart did not have long tube peices and I didn't feel like buying any because I had so much other stuff just laying around. Hence a new design ( no drawings.)
Here are some more recent photos
Here are some more recent photos
The idea
The main idea with this machine and what will set it apart from others is that it is basically a universal cartesian prototyping machine. All modules on the machine run on basic G-code and several of them attach to other modules. For example the Router not only routes but can do light milling with the speed turned down and a fixture plate slipped into the base. Putting the 3D scanning bed in the base, attaching the camera, turning the laser on and running certain code allows it to scan in 3D with David 3D scanner software. Putting a stencil cutter fixture in the router collet allows it to cut vinyl or paper, etc. On one end of the machine the rapid prototyping module rests while not in use but can be used in the same envelope for printing, pick and place operations etc. The other reason for separating the Rep Rap based prototyper is that it has been designed for lightness and speed while the larger module is designed for cutting at slower speeds ( still pretty fast) in heavier materials up to and including light iron and steel.
I bought a lot of parts on Ebay over the last year and generally saved for other material. I decided to lease the space with my wife and kids and sort of split it up between clean and dirty areas. We had to frame out space into a large existing multilevel warehouse.
We scored big time in other ways by leasing the space. The owner of the building co-owns a hair blending company that makes custom blends for brooms, brushes, etc. and happened to be getting rid of some old machines. These machines contained a plethura of 80/20 aluminum, PLC's, linear motion components, motors, gears, pneumatic devices and controls etc. I was able to augment and drastically improve the machine by using these materials.
Here are some photos of the raw material
Subscribe to:
Posts (Atom)